A wide variety of
Technical Services
Ad Hoc Marine Designs Ltd. is design Consultancy Company that offers a wide variety of technical services.
Offering Naval Architecture, Marine, Structural, Hydrodynamic and first principal design calculations and calculations in all things High Speed and novel, ranging from: Paramilitary; Workboat; Crew Boat; Patrol boat and marine related structures such as pontoons world wide.
With over 60 years of collective experience in shipyard production and design, we offer practical hands-on advice in all aspect of marine design and naval architecture as well as onsite support.
Being authors of many international technical papers text books and being a member of Lloyd’s Register’s Technical Committee, we are able to draw upon our vast technical resources for quick effective problem solving that offers a wide variety of technical services. Find out more below.
With over 60 years of collective experience in shipyard production and design, we offer practical hands-on advice in all aspect of marine design and naval architecture as well as onsite support.
Being authors of many international technical papers text books and being a member of Lloyd’s Register’s Technical Committee, we are able to draw upon our vast technical resources for quick effective problem solving that offers a wide variety of technical services. Find out more below.
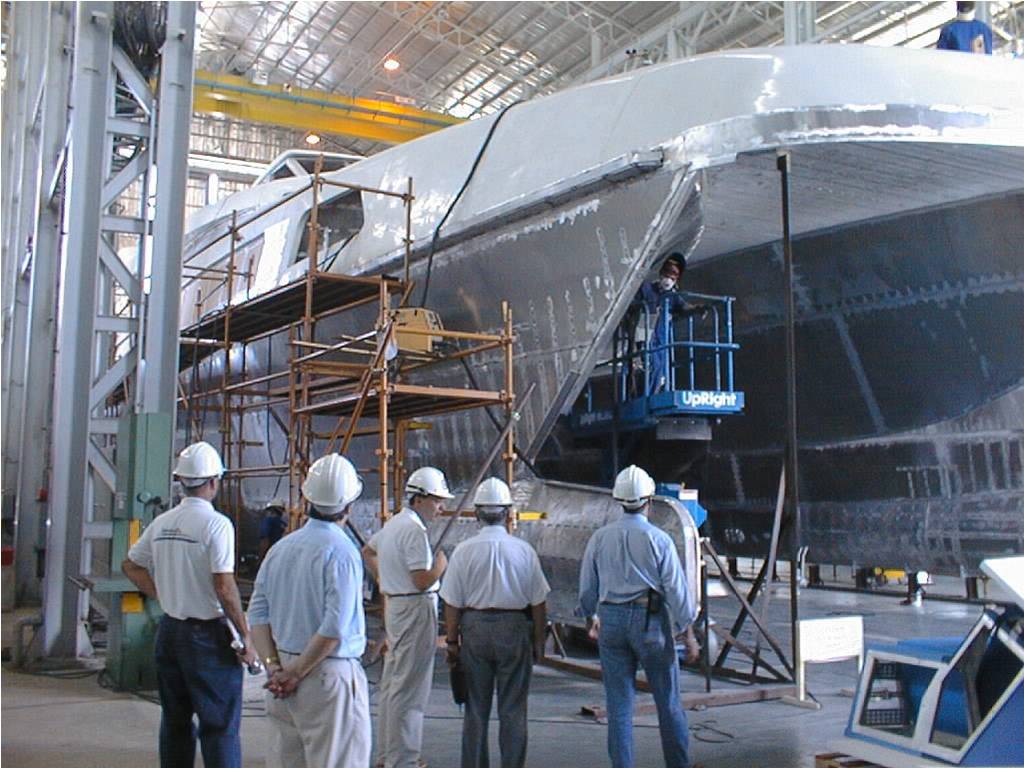
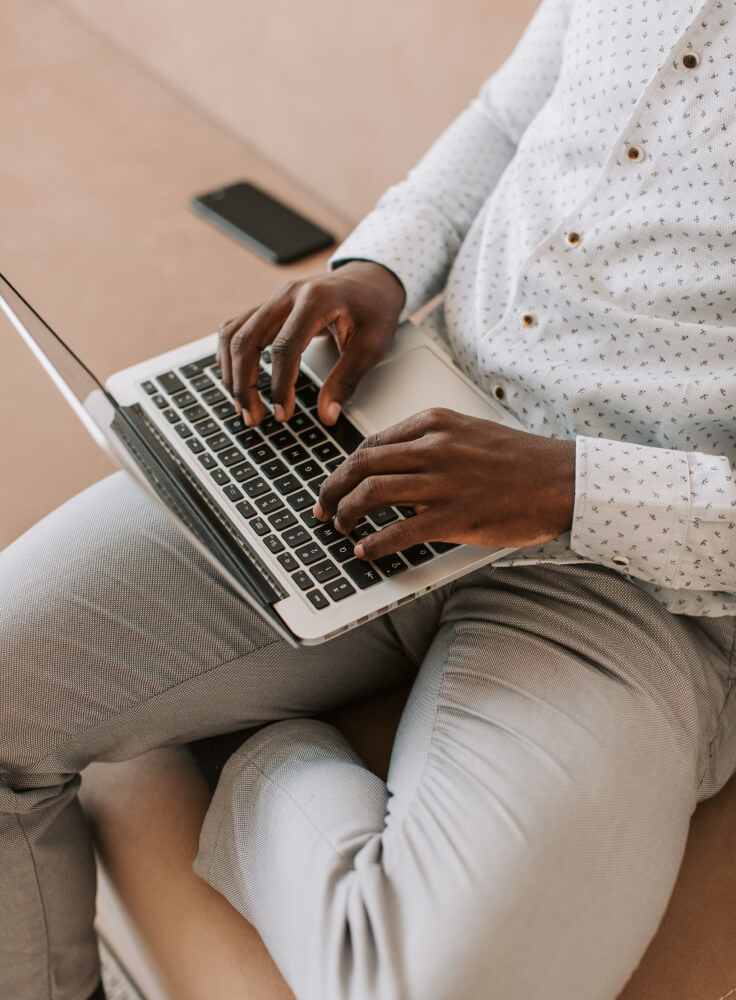
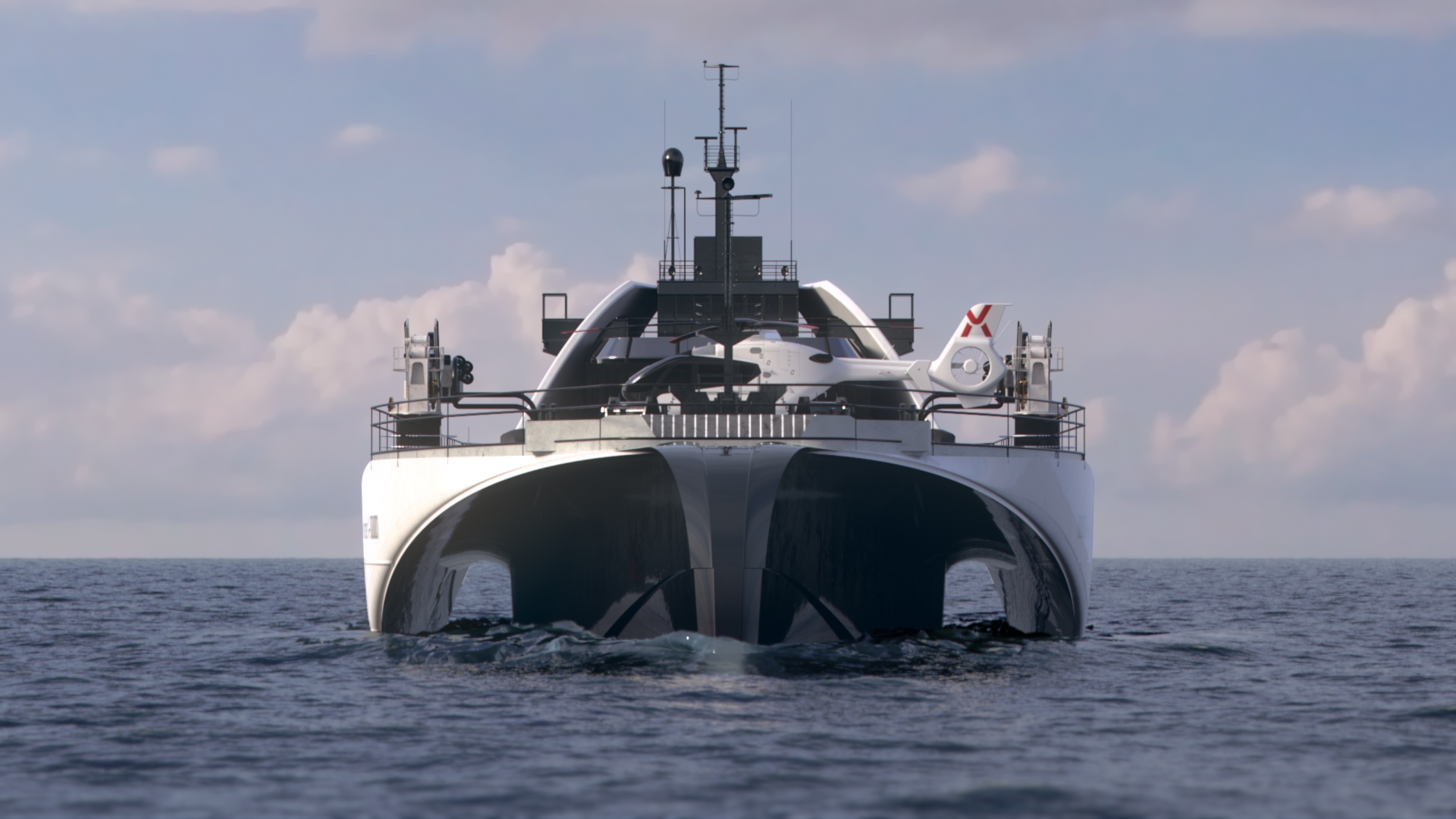
Concept design of specialised craft
We specialise in novel concepts. Creating concepts that are sometimes beyond the envelope of generally accepted naval architecture as well as using existing philosophies to design vessels that offer a unique role.
Specialist in Structural Design and Fabrication
Whether a small lifting eye, or a conversion of a large RoPax vessel or the structural design of high speed patrol boats, Ad Hoc Marine Designs offer detailed structural analysis from first principals to Class rules compliance. We are known as the go-to experts in aluminium design and fabrication.
John Kecsmar’s expertise is noted by his many publications whether technical peer reviewed papers or his many contributions to articles published in Professional Boatbuilder magazine.
John Kecsmar’s expertise is noted by his many publications whether technical peer reviewed papers or his many contributions to articles published in Professional Boatbuilder magazine.
FE Analysis
John Kecsmar has been using FEA since the early 1990s to validate first principal calculations as well as research into fatigue hot spot stresses in details design.
The most common reason for using FEA is establishing global stresses on multihull vessels, to facilitate the detailed structural design. It allows for quick iterative options and investigating different scenarios quickly. Using FEA on detailed joint analysis to identify problem areas and stress concentrations using fatigue and FAT categories for improved fatigue resistant structures.
The most common reason for using FEA is establishing global stresses on multihull vessels, to facilitate the detailed structural design. It allows for quick iterative options and investigating different scenarios quickly. Using FEA on detailed joint analysis to identify problem areas and stress concentrations using fatigue and FAT categories for improved fatigue resistant structures.
Construction Advice
We can advise on just about any method of construction whether it is for a new build or a repair or general advice. Structural design is not just about calculation, it is about ease of fabrication. Being heavily involved with a shipyard, implications on cost, time and quality of the fabrication are often at variance with the design intent. As such, this often requires a unique solution to each problem.
Specialist in SWATH
The design team of Ad Hoc Marine Designs were responsible for the concept and detailed design of two highly successful SWATHs, PATRIA and the two smaller PTC SWATHs operating out of Plymouth UK all built by FBM Marine. The latter was a subject of two RINA papers- International Symposium on the Safety of High Speed Craft 6th and 7th Feb. 1997 and SURV 6 Conference 17-18th March 2004. Patria at 32 knots is still the fastest SWATH in the world, after 30 years’ service she is now operating out of the Philippines.
Ad Hoc Marine Designs Ltd owing to their expertise in Swath hull forms and aluminium design were selected to provide all the naval architectural design for the Lockheed Martin SWATH of the SLICE© vessel, built at FBMA in 2006.
Ad Hoc’s current world beating Typhoon range of CTV SWATHs are plying the waters of the North Sea. These superior seakeeping vessels have added an additional 90 days per year to the operational window of the CTV for their operator, MCS (Clyde) Ltd. delivering world class performance of operating in Hs=3.5m seas with less than 0.10g vertical accelerations and tower transfers up to Hs=2.5m. When pushing onto the tower the Capt’s note: They stick like Velcro!
Ad Hoc Marine Designs Ltd owing to their expertise in Swath hull forms and aluminium design were selected to provide all the naval architectural design for the Lockheed Martin SWATH of the SLICE© vessel, built at FBMA in 2006.
Ad Hoc’s current world beating Typhoon range of CTV SWATHs are plying the waters of the North Sea. These superior seakeeping vessels have added an additional 90 days per year to the operational window of the CTV for their operator, MCS (Clyde) Ltd. delivering world class performance of operating in Hs=3.5m seas with less than 0.10g vertical accelerations and tower transfers up to Hs=2.5m. When pushing onto the tower the Capt’s note: They stick like Velcro!
Specialist in Catamaran & Low Wash Naval Architecture
Many variations of high speed catamaran hull form have been model tested for resistance including variations in beam to draft ratio, length to beam and hull shape from semicircular section to rectangular section. A unique easy-to-build flat bottom, rectangular shape has also been tested. Coupled to this research was the investigation into low wash hull forms. This resulted in the concept and detail design of the three low wash 23m high speed riverbus catamaran craft operating on the Thames UK and three 15m monhull fast passenger launches also operating on the Thames designed and built at FBM Marine.
Specialist in CTV designs
Ad Hoc Marine Designs with TT Boat designs were the silent naval architects in principal design and technical DNA behind the highly successful range of South Boat Catamarans built on the Isle of Wight, up into 2012. This included designing their now unique flexibly mounted deckhouse.
Additional services
Additional services include:
- Rapid resistance model testing & comparative studies
- Corrosion advice
- Re-Engining advice
- Independent trial analysis and advice on rectification
- Independent design reviews
- Heavy lift arrangements
- On-site technical design support
- Customer Representation
- Repair and Redesign work
- Safety Case studies
- Inclining Experiments & Stability Analysis
- Rapid resistance model testing & comparative studies
- Corrosion advice
- Re-Engining advice
- Independent trial analysis and advice on rectification
- Independent design reviews
- Heavy lift arrangements
- On-site technical design support
- Customer Representation
- Repair and Redesign work
- Safety Case studies
- Inclining Experiments & Stability Analysis